
Understanding the Basics
Spot Welding: Definition and Process
Spot welding is a prominent technique in joining metal surfaces. It primarily involves applying pressure and heat generated by electric current to weld contact points on overlapping pieces. The equipment used in spot welding generally includes an apparatus known as a spot welder, which is proficient in delivering controlled pulses of electricity through electrodes to create a weld. This method finds extensive applications in industries such as automotive manufacturing, electronics, and sheet metal production.
Traditional Welding: Definition and Process
Traditional welding encompasses various methods, including MIG (Metal Inert Gas), TIG (Tungsten Inert Gas), and Arc welding. These techniques involve melting base materials with targeted heat application usually derived from an electrical source or gas flame and adding filler material for joint strength. Equipment ranges from simple hand-held torches to complex automated systems. They are fundamental in sectors like construction, aerospace, and shipbuilding due to their versatility and efficacy across numerous applications.
Efficiency and Speed
Spot Welding Efficiency
The efficiency and speed of spot welding are notable assets. Due to its rapid cycle time, often taking mere milliseconds per weld, this method can significantly enhance production rates. Its compatibility with automation amplifies throughput even further. Case studies from the automotive industry demonstrate how integrating robotic spot welding has revolutionized assembly line productivity and reduced labor costs.
Traditional Welding Efficiency
In contrast, traditional welding techniques require more setup and preparation but offer flexibility that spot welding lacks. For instance, they are suitable for diverse geometries and sizes, making them adaptable to varied project requirements. Real-world examples abound, highlighting instances where traditional welding facilitated major infrastructure projects efficiently despite longer individual weld times compared to spot welding.
Material Compatibility
Materials Best Suited for Spot Welding
Spot welding excels with specific types of metals, particularly thin sheets of steel and aluminum up to around 3mm thick. However, this process does come with limitations—it struggles with thicker materials and metals with high thermal conductivity or those prone to cracking under localized heat treatment. Nonetheless, adhering strictly to compatible materials ensures optimal results.
Materials Best Suited for Traditional Welding
Traditional welding proudly boasts broader applicability regarding materials and thicknesses. From ferrous to non-ferrous metals spanning considerable thickness ranges, these methods tackle a variety of tasks seamlessly. Despite potential challenges such as distortion control in thin sheets, proper settings and expertise help overcome obstacles, broadening the spectrum of feasible materials considerably.
Strength and Durability
Strength of Spot Welds
A quintessential boon of spot welding lies in its strength metrics, especially tensile and shear strengths, making it ideal for high-stress applications like vehicle chassis. The durability over long-term use evidenced by thorough testing establishes trust in critical operations. Comprehensive test methodologies uniformly substantiate the reliability of spot welds against stringent performance benchmarks.
Strength of Traditional Welds
Comparatively, traditional welds demonstrate impressive strength, frequently exceeding those achieved by spot welding depending on scenario specifics. Their capacity to endure varying conditions—from extreme temperatures to corrosive environments—positions them favorably across disparate industries. Routine testing confirms that, when executed properly, traditional welds meet rigorous durability standards consistently.
Cost Considerations
Cost of Spot Welding
The initial investment for spot welding equipment could be significant, yet operational expenses tend to balance out in mass production contexts due to faster cycles reducing labor requirements. Maintenance costs remain manageable, contributing positively to overall expense profiles, particularly when considering the lifespan of robust machinery designed explicitly for heavy-duty performance.
Cost of Traditional Welding
Traditional welding implies variable costing patterns encompassing higher expenditures initially on versatile equipment and ongoing operational costs influenced by factors such as consumables and skilled labor wages. While potentially escalating maintenance needs might inflate budgets slightly, contextual economic evaluations reveal favorable cost-efficiency landscapes under numerous circumstances.
Safety and Environmental Impact
Safety Concerns in Spot Welding
Common safety issues in spot welding revolve around exposure to electrical hazards and hot work zones. Proper mitigative strategies include adequate personal protective equipment (PPE) ranging from gloves to eye shields. Considering environmental impact, spot welding tends to be relatively sustainable given less requisite consumable usage compared to other welding forms.
Safety Concerns in Traditional Welding
Traditional welding introduces multiple hazards, prominently ultraviolet radiation, intense heat, and airborne contaminants necessitating comprehensive PPE adoption including respirators and welding helmets. Nevertheless, advancements seeking greener technologies mitigate some environmental impacts associated with consumable depletion and emissions typically characterizing conventional practices.
Skill Level and Training
Training Requirements for Spot Welding
Spot welding demands intermediate skill levels largely based on understanding machine operation rather than intricate manual dexterity. Accessible training programs prepare technicians adequately, ensuring certification processes align practical knowledge with contemporary industrial requisites.
Training Requirements for Traditional Welding
Traditional welding mandates varied proficiency tiers contingent on specific methods and applicable project dimensions. Intensive training regimes incorporating theoretical instruction along with hands-on practice equip individuals extensively, validating competence via recognized credentials indicative of expert-level mastery.
Case Studies and Real-World Applications
Examples of Spot Welding in Industry
The automotive sector leverages spot welding predominantly; automobile makers epitomize its utility in fabricating unibody structures swiftly. Similarly, electronic manufacturers employ it for producing resilient circuit connections necessary within intricate devices ubiquitously encountered globally.
Examples of Traditional Welding in Industry
Construction undertakings exemplify reliance on traditional welding, where erecting stable frameworks requires robust joint integrity. Aerospace components fashioned utilizing advanced TIG/MIG processes affirm precision adherence while maritime domains commend traditional welding’s resilience amidst challenging aquatic environments.
Future Trends and Innovations
Innovations in Spot Welding Technology
Progressive trends accentuate enhanced electrode management systems coupled with smarter integration capabilities facilitating superior quality control and efficiency gains. Speculative outlooks envisage seamless connectivity fostering synchronized multi-unit operations carving futuristic pathways forward.
Innovations in Traditional Welding Technology
Conventional welding technological strides underscore breakthroughs such as friction stir welding expanding feasibility scopes alongside refined automation robotics harmonizing operational synchrony usher dynamic evolution continuously transforming landscape paradigms.
Making the Choice
Determining whether to integrate spot welding or traditional welding anchors fundamentally on specific project imperatives balanced against multifarious considerations. Project scale, required finesse, budget constraints intertwined with expected outputs guide decision matrices critically impacting successful implementation strategy formulations ensuring optimal results attainment.
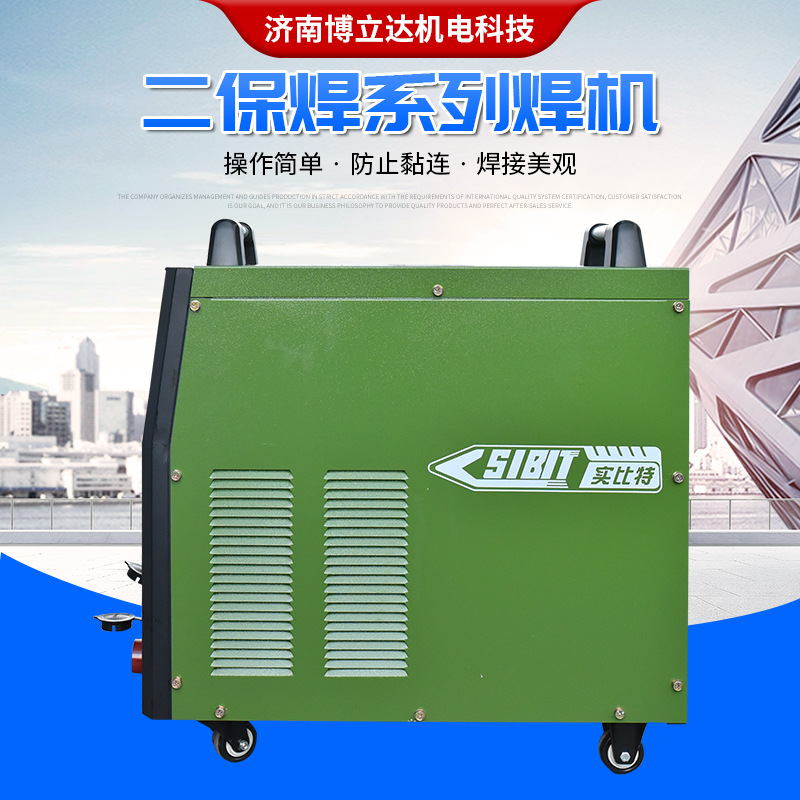