
At the heart of modern manufacturing lies a process so pivotal yet so intricate that it has shaped the future of production across industries. Spot welding, a technique used to join materials, typically metals, through the application of pressure and heat delivered at their interface through electrodes, has been a cornerstone of manufacturing for over a century. Its evolution from a manually intensive process to a highly sophisticated, automated operation underscores the technological advancements that have permeated the manufacturing sector.
The historical journey of spot welding from its rudimentary beginnings to the advanced techniques in use today reflects a broader narrative of innovation and progress. Initially developed for the automotive industry in the early 20th century, spot welding has undergone significant transformations, adapting to the needs of various sectors and benefiting from technological advancements, particularly in the realms of materials science and electrical engineering.
Enter GTPOWER, a name that has become synonymous with cutting-edge spot welding technology. GTPOWER has introduced innovations that have not only enhanced the efficiency and reliability of spot welding but have also set new standards for the industry. With its focus on developing industrial-grade welding and cutting machines that provide seamless integration of spot welding and carbon dioxide gas welding protection, GTPOWER is revolutionizing how manufacturers approach welding tasks.
The key features of GTPOWER's spot welding solutions, such as precision control, energy efficiency, and user-friendly interface, contribute significantly to the enhanced speed and efficiency in manufacturing. These advancements ensure unparalleled reliability and quality of welds, meeting the rigorous standards of modern production lines. Moreover, the environmental benefits of these modern spot welding methods cannot be overstated, as they offer a cleaner, more sustainable alternative to traditional welding techniques.
Spot welding's versatility is evident in its wide range of application areas. In the automotive industry, for example, it plays a critical role in assembling vehicle bodies, ensuring structural integrity and safety. The electronics and precision engineering sectors rely on spot welding for the miniaturization of components, where traditional welding methods would prove cumbersome or impractical. Similarly, the construction and heavy machinery industries benefit from the robustness and durability of spot-welded joints.
However, the journey of integrating advanced spot welding techniques such as those offered by GTPOWER is not without its challenges. Manufacturers often face issues related to equipment cost, operational complexity, and the need for specialized training. GTPOWER addresses these issues head-on, providing solutions that are not only technologically advanced but also accessible and user-friendly, ensuring a smooth transition for manufacturers looking to upgrade their welding operations.
Looking ahead, the future of manufacturing with spot welding technology appears bright, with trends indicating a move towards greater automation and the integration of artificial intelligence (AI). These technologies promise to further enhance the efficiency, precision, and cost-effectiveness of spot welding, making it an even more indispensable part of manufacturing. GTPOWER is at the forefront of these developments, continuously exploring new ways to innovate and improve upon its spot welding solutions.
Real-world success stories abound, highlighting companies that have transformed their manufacturing processes through the adoption of GTPOWER spot welding technology. These stories not only serve as a testament to the effectiveness of GTPOWER's solutions but also provide valuable insights and lessons for other manufacturers considering a similar path.
For manufacturers navigating the adoption of advanced spot welding solutions, considerations such as compatibility with existing production lines, cost-benefit analysis, and potential disruptions to operations are paramount. GTPOWER assists in this transition by offering comprehensive support, from initial consultation to post-implementation training and maintenance. This ensures that manufacturers can confidently integrate GTPOWER technologies, securing a competitive advantage in their respective markets.
In reflection, the path forward for manufacturers is clear: embracing innovation in welding, particularly spot welding technology, is not just a means to improve operational efficiency but a strategic move to stay ahead in an increasingly competitive and fast-paced industry. With the continuous evolution of spot welding technology, led by pioneers like GTPOWER, the future of manufacturing looks not only more efficient and sustainable but also infinitely more promising.
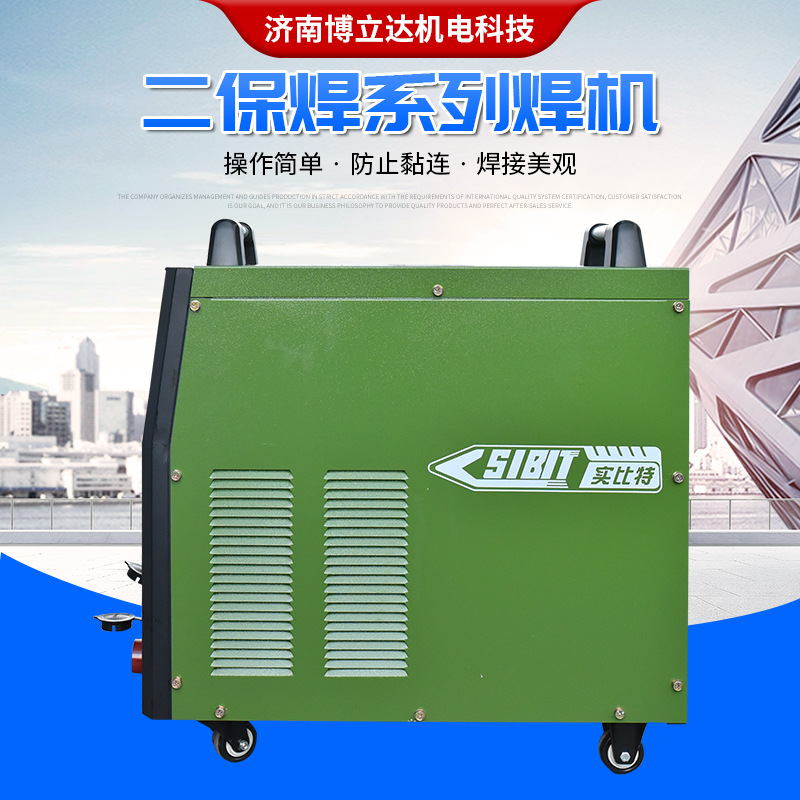